Os métodos de revestimento de fotoresist divídense xeralmente en revestimento por centrifugado, revestimento por inmersión e revestimento en rollo, entre os que o revestimento por centrifugado é o máis utilizado. Mediante o revestimento por centrifugado, o fotorresistente gotea sobre o substrato e o substrato pódese xirar a alta velocidade para obter unha película de fotorresistencia. Despois diso, pódese obter unha película sólida quentándoa nunha placa quente. O revestimento por centrifugado é adecuado para recubrir desde películas ultrafinas (uns 20 nm) ata películas grosas duns 100 um. As súas características son unha boa uniformidade, un grosor de película uniforme entre as obleas, poucos defectos, etc., e pódese obter unha película con alto rendemento de revestimento.
Proceso de revestimento por centrifugado
Durante o revestimento por centrifugación, a velocidade de rotación principal do substrato determina o grosor da película da fotoresistencia. A relación entre a velocidade de rotación e o espesor da película é a seguinte:
Spin = kTn
Na fórmula, Spin é a velocidade de rotación; T é o espesor da película; k e n son constantes.
Factores que afectan o proceso de revestimento por centrifugado
Aínda que o grosor da película está determinado pola velocidade de rotación principal, tamén está relacionado coa temperatura ambiente, a humidade, a viscosidade do fotorresistente e o tipo de fotorresistencia. Na Figura 1 móstrase a comparación de diferentes tipos de curvas de revestimento fotorresistente.
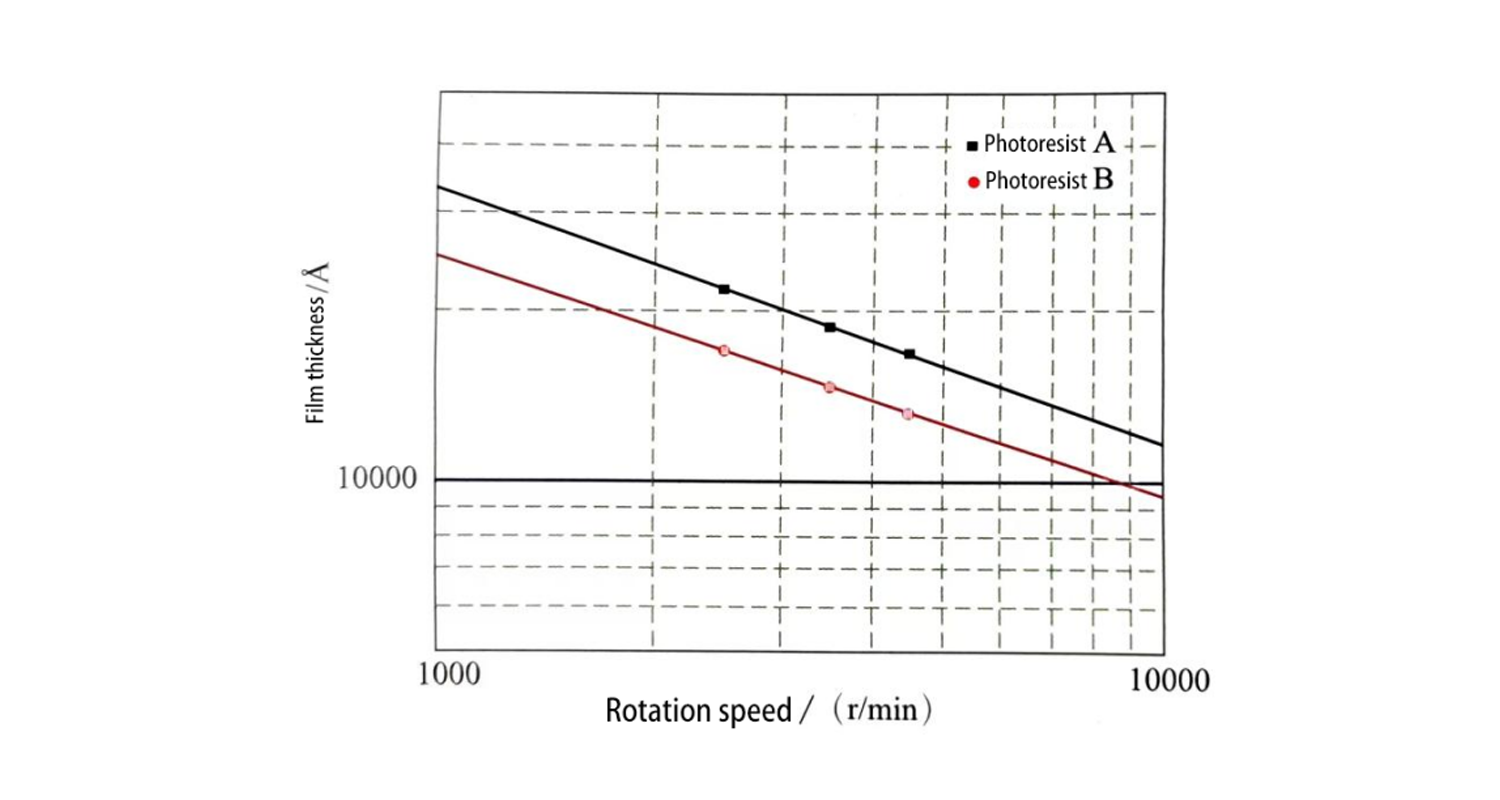
Figura 1: Comparación de diferentes tipos de curvas de revestimento fotorresistente
Influencia do tempo de rotación principal
Canto máis curto sexa o tempo de rotación principal, maior será o grosor da película. Cando se aumenta o tempo de rotación principal, a película se fai máis fina. Cando supera os 20 segundos, o grosor da película permanece case inalterado. Polo tanto, o tempo de rotación principal adoita seleccionarse para ser superior a 20 segundos. A relación entre o tempo de rotación principal e o espesor da película móstrase na Figura 2.
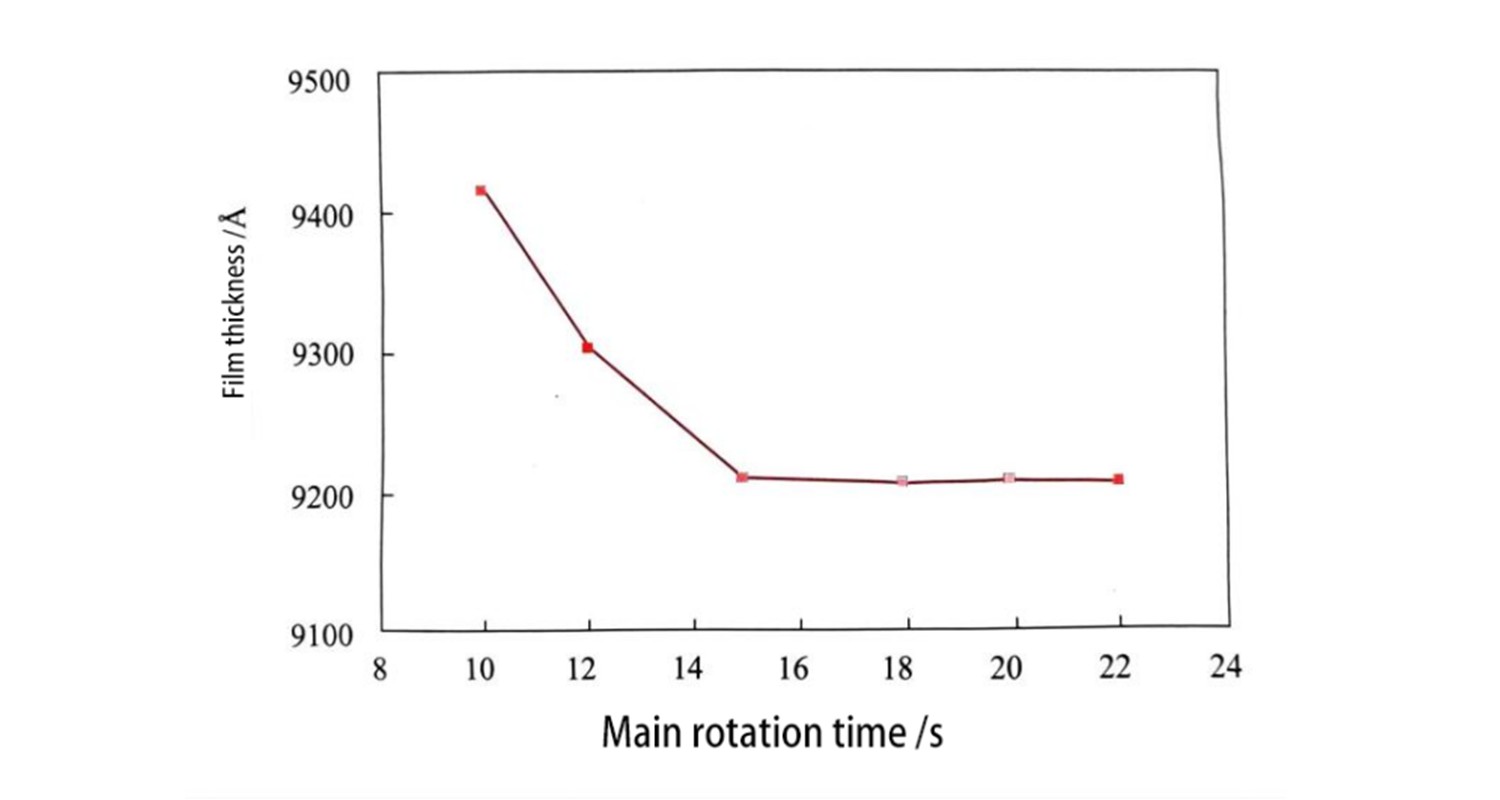
Figura 2: Relación entre o tempo de rotación principal e o espesor da película
Cando o fotorresistente gotea sobre o substrato, aínda que a velocidade de rotación principal posterior sexa a mesma, a velocidade de rotación do substrato durante o goteo afectará ao espesor final da película. O espesor da película fotorresistente aumenta co aumento da velocidade de rotación do substrato durante o goteo, o que se debe á influencia da evaporación do disolvente cando o fotorresistente se desprega despois do goteo. A figura 3 mostra a relación entre o espesor da película e a velocidade de rotación principal a diferentes velocidades de rotación do substrato durante o goteo da fotoresistencia. A partir da figura pódese ver que co aumento da velocidade de rotación do substrato de goteo, o grosor da película cambia máis rápido e a diferenza é máis obvia na zona con menor velocidade de rotación principal.
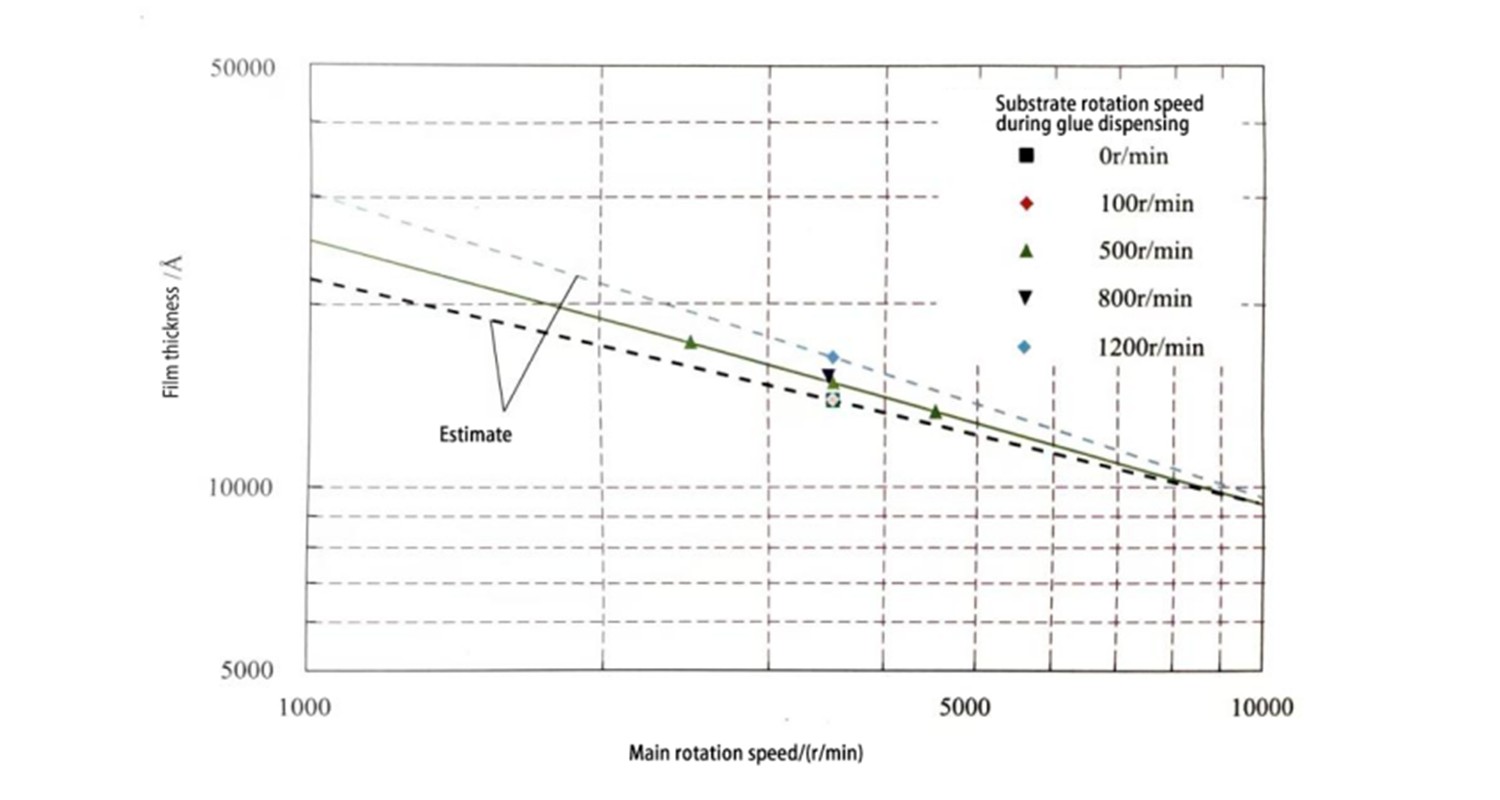
Figura 3: Relación entre o espesor da película e a velocidade de rotación principal a diferentes velocidades de rotación do substrato durante a dispensación de fotorresistente
Efecto da humidade durante o revestimento
Cando a humidade diminúe, o espesor da película aumenta, porque a diminución da humidade favorece a evaporación do disolvente. Non obstante, a distribución do espesor da película non cambia significativamente. A figura 4 mostra a relación entre a humidade e a distribución do espesor da película durante o revestimento.
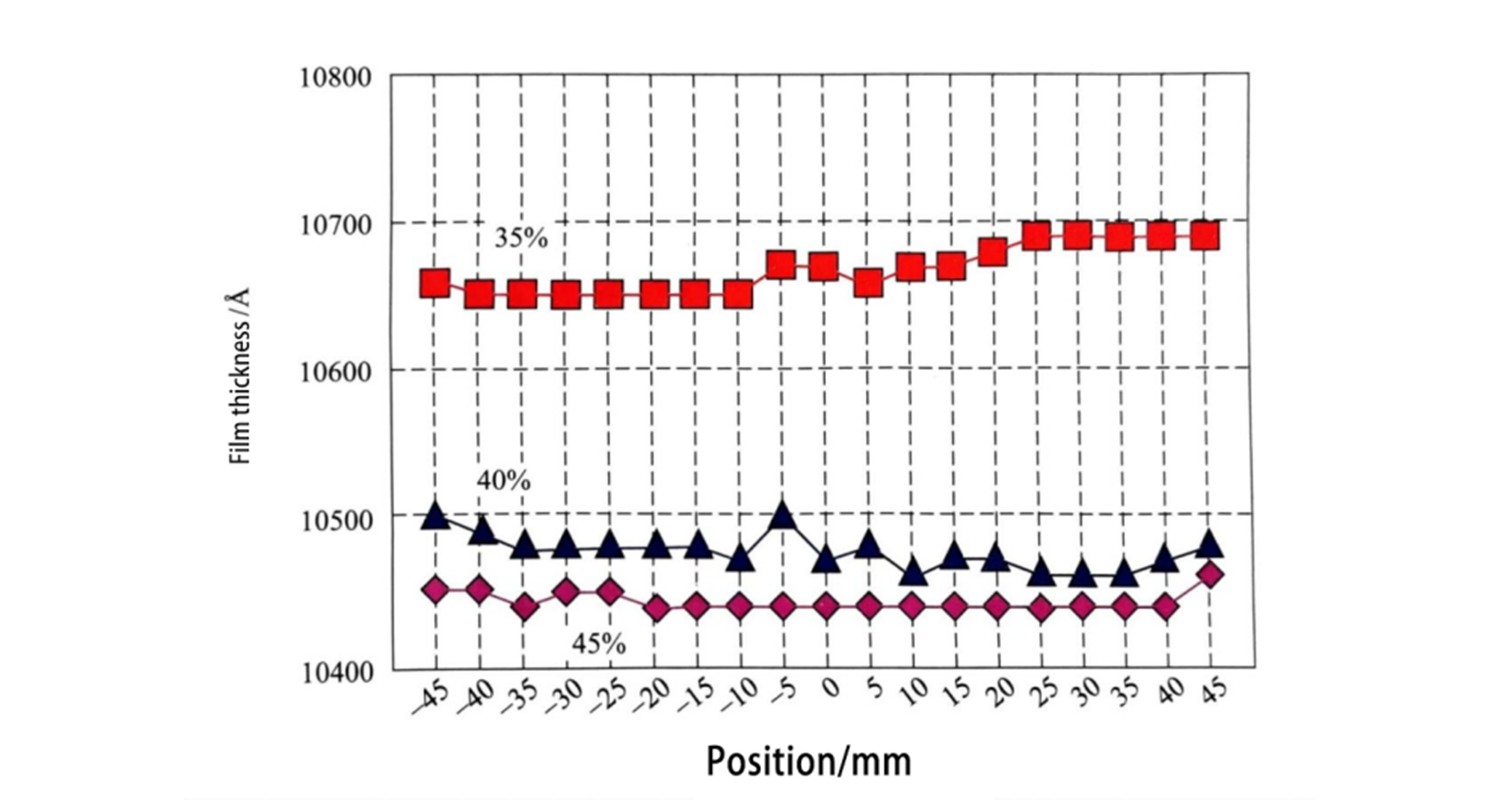
Figura 4: Relación entre a humidade e a distribución do espesor da película durante o revestimento
Efecto da temperatura durante o revestimento
Cando a temperatura interior aumenta, o grosor da película aumenta. Pódese ver na Figura 5 que a distribución do espesor da película fotorresistente cambia de convexa a cóncava. A curva da figura tamén mostra que a maior uniformidade se obtén cando a temperatura interior é de 26 °C e a temperatura de fotorresistencia é de 21 °C.
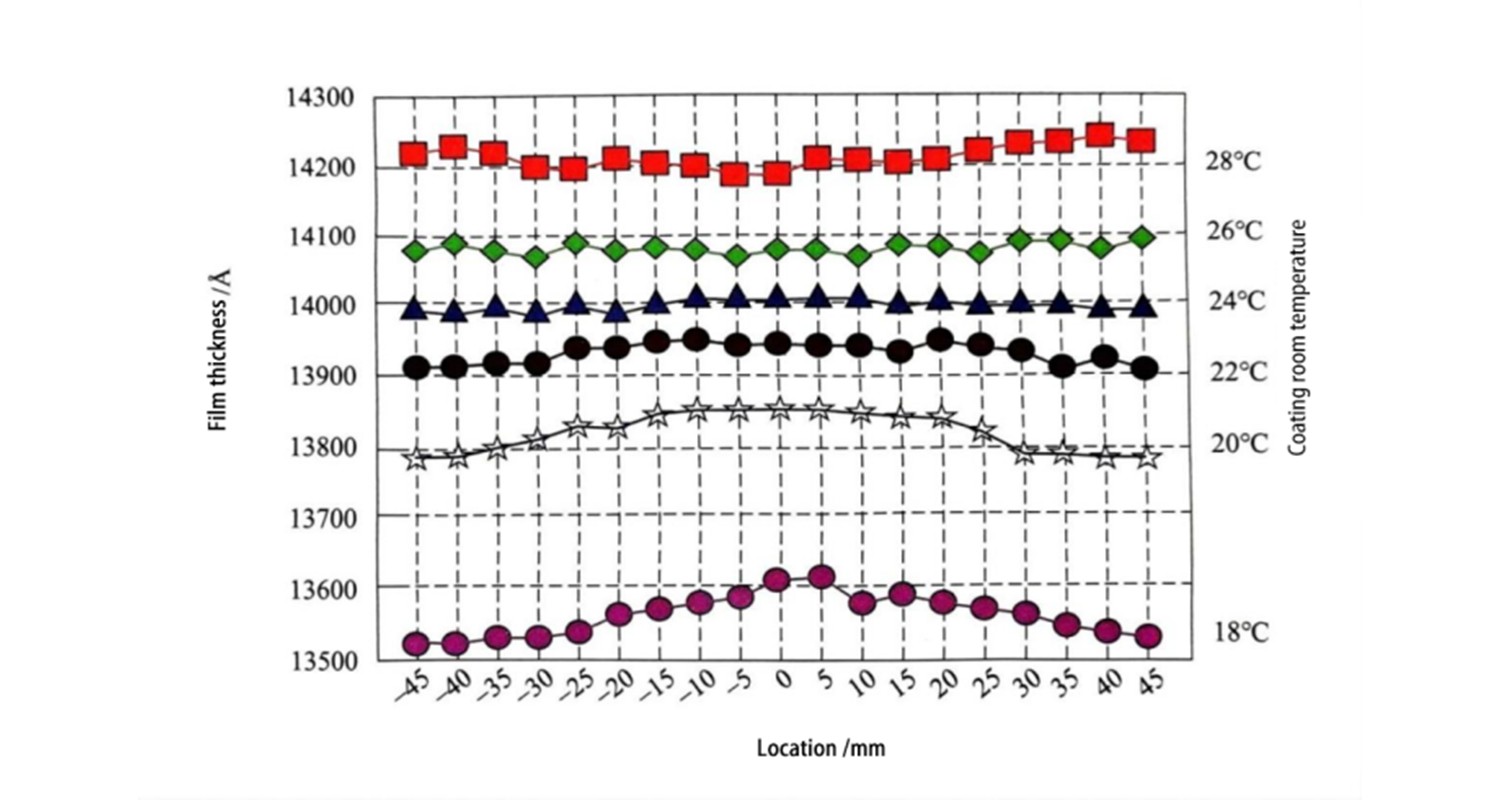
Figura 5: Relación entre a temperatura e a distribución do espesor da película durante o revestimento
Efecto da velocidade de escape durante o revestimento
A figura 6 mostra a relación entre a velocidade de escape e a distribución do espesor da película. En ausencia de escape, mostra que o centro da oblea tende a engrosar. Aumentar a velocidade de escape mellorará a uniformidade, pero se se aumenta demasiado, a uniformidade diminuirá. Pódese ver que existe un valor óptimo para a velocidade de escape.
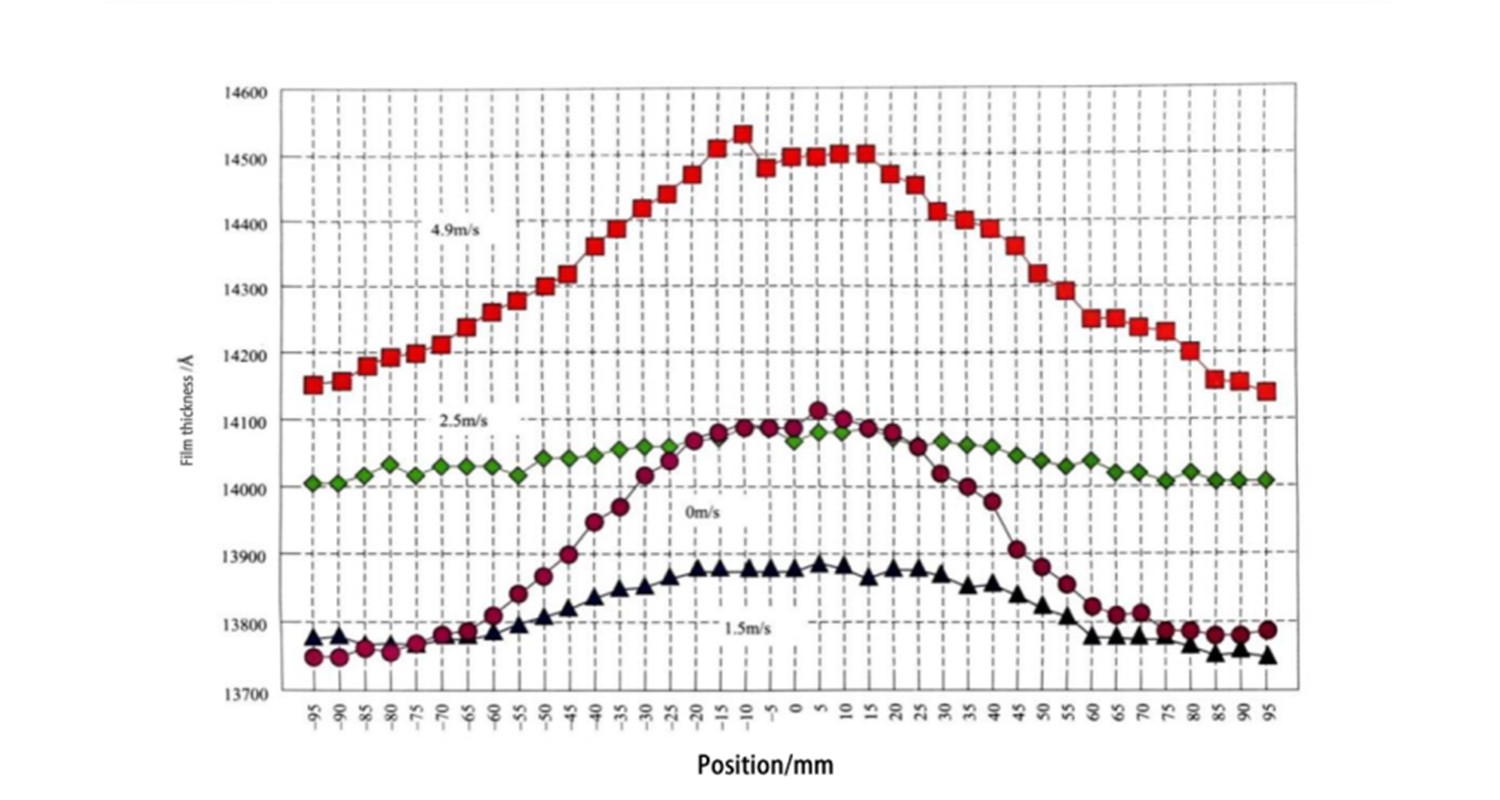
Figura 6: Relación entre a velocidade de escape e a distribución do espesor da película
Tratamento HMDS
Para que o fotorresistente sexa máis revestible, a oblea debe ser tratada con hexametildisilazano (HMDS). Especialmente cando a humidade está unida á superficie da película de óxido de Si, fórmase silanol, o que reduce a adhesión do fotorresistente. Para eliminar a humidade e descompoñer o silanol, a oblea normalmente quéntase a 100-120 °C e introdúcese a néboa HMDS para provocar unha reacción química. O mecanismo de reacción móstrase na figura 7. A través do tratamento con HMDS, a superficie hidrófila cun pequeno ángulo de contacto convértese nunha superficie hidrófoba cun gran ángulo de contacto. O quecemento da oblea pode obter unha maior adhesión do fotorresistente.
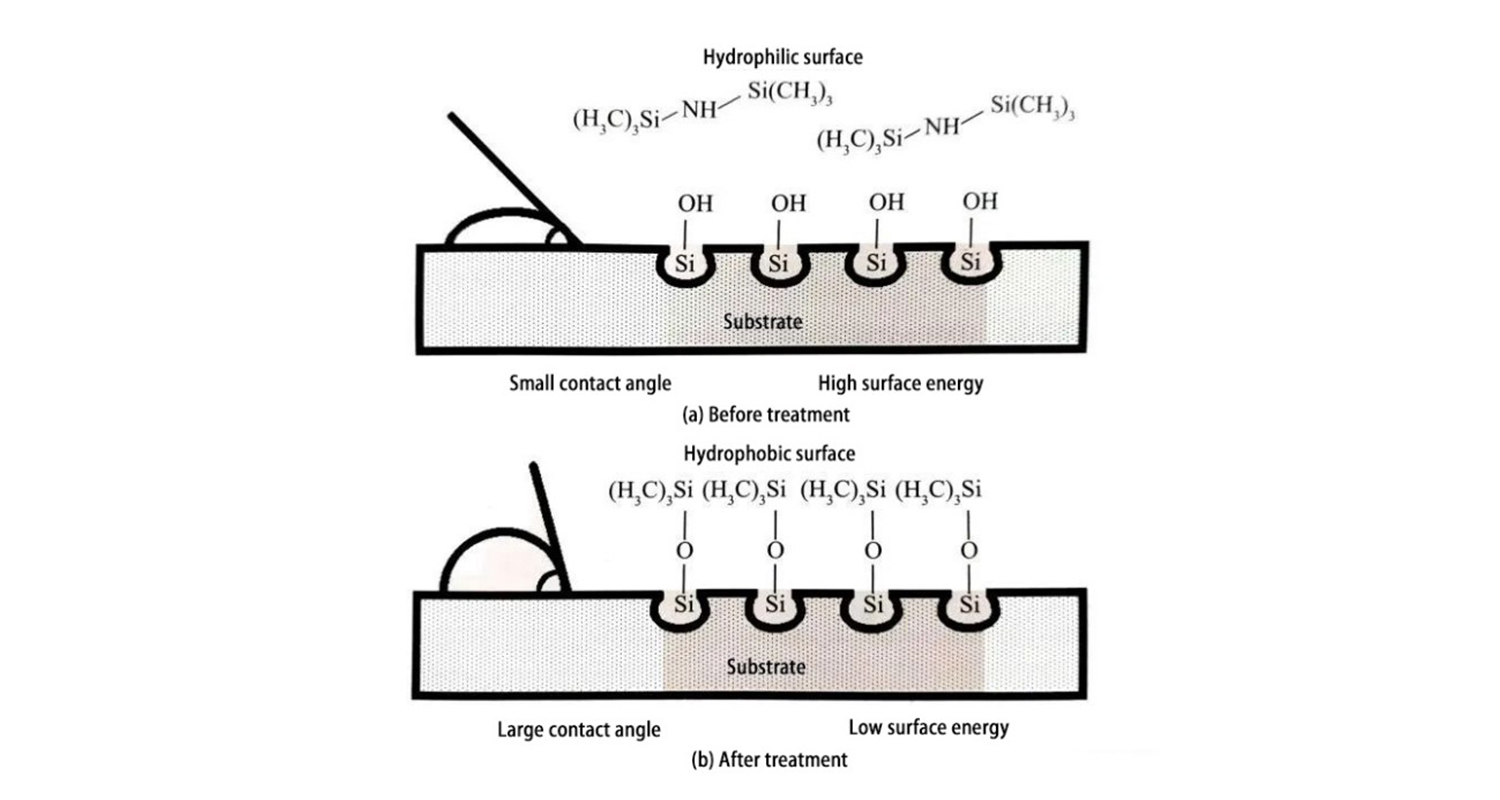
Figura 7: mecanismo de reacción HMDS
O efecto do tratamento con HMDS pódese observar medindo o ángulo de contacto. A figura 8 mostra a relación entre o tempo de tratamento do HMDS e o ángulo de contacto (temperatura de tratamento 110 °C). O substrato é Si, o tempo de tratamento HMDS é superior a 1 min, o ángulo de contacto é superior a 80 ° e o efecto do tratamento é estable. A figura 9 mostra a relación entre a temperatura de tratamento do HMDS e o ángulo de contacto (tempo de tratamento 60 s). Cando a temperatura supera os 120 ℃, o ángulo de contacto diminúe, o que indica que o HMDS se descompón debido á calor. Polo tanto, o tratamento con HMDS adoita realizarse a 100-110 ℃.
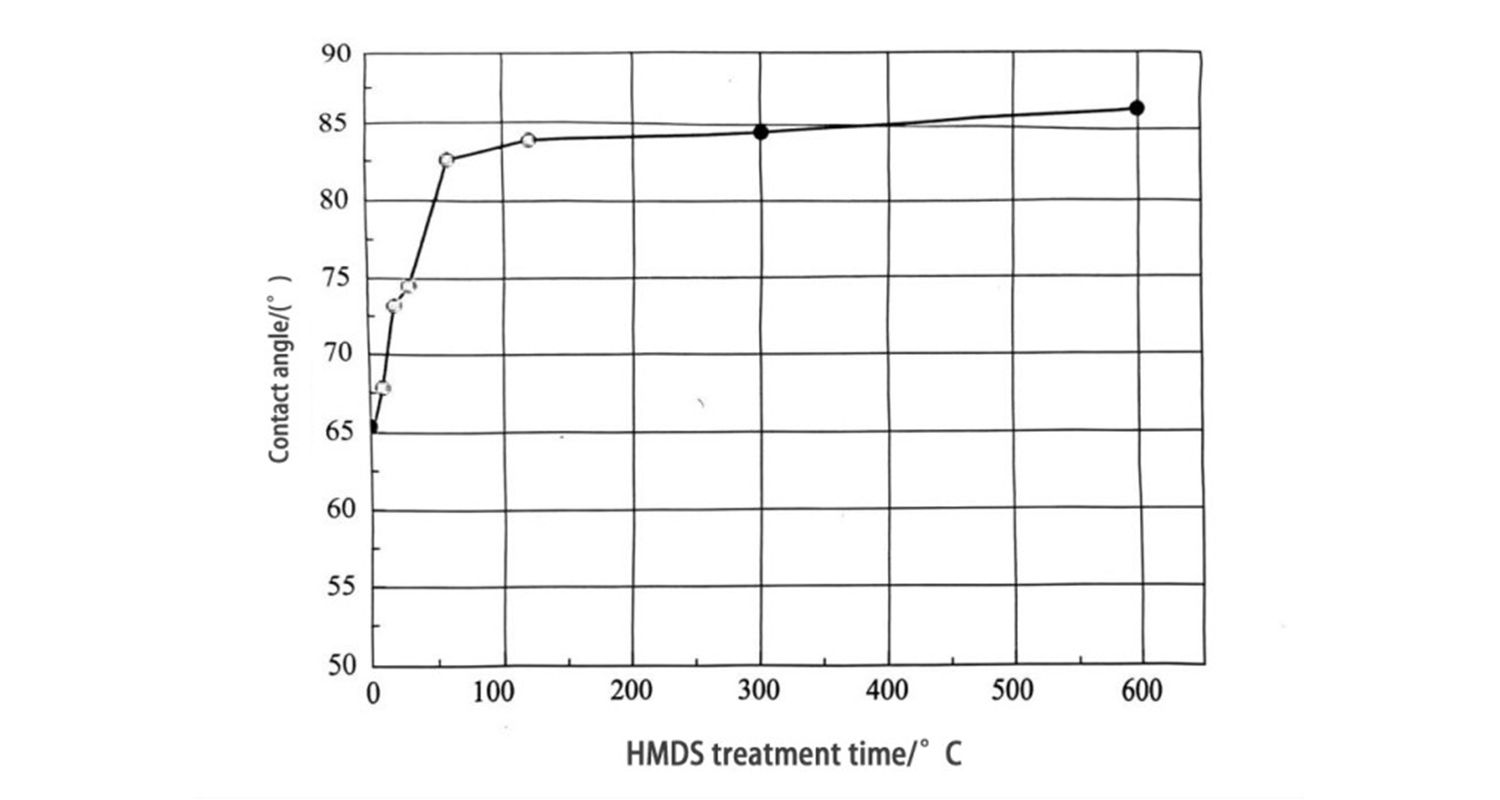
Figura 8: Relación entre o tempo de tratamento do HMDS
e ángulo de contacto (temperatura de tratamento 110 ℃)
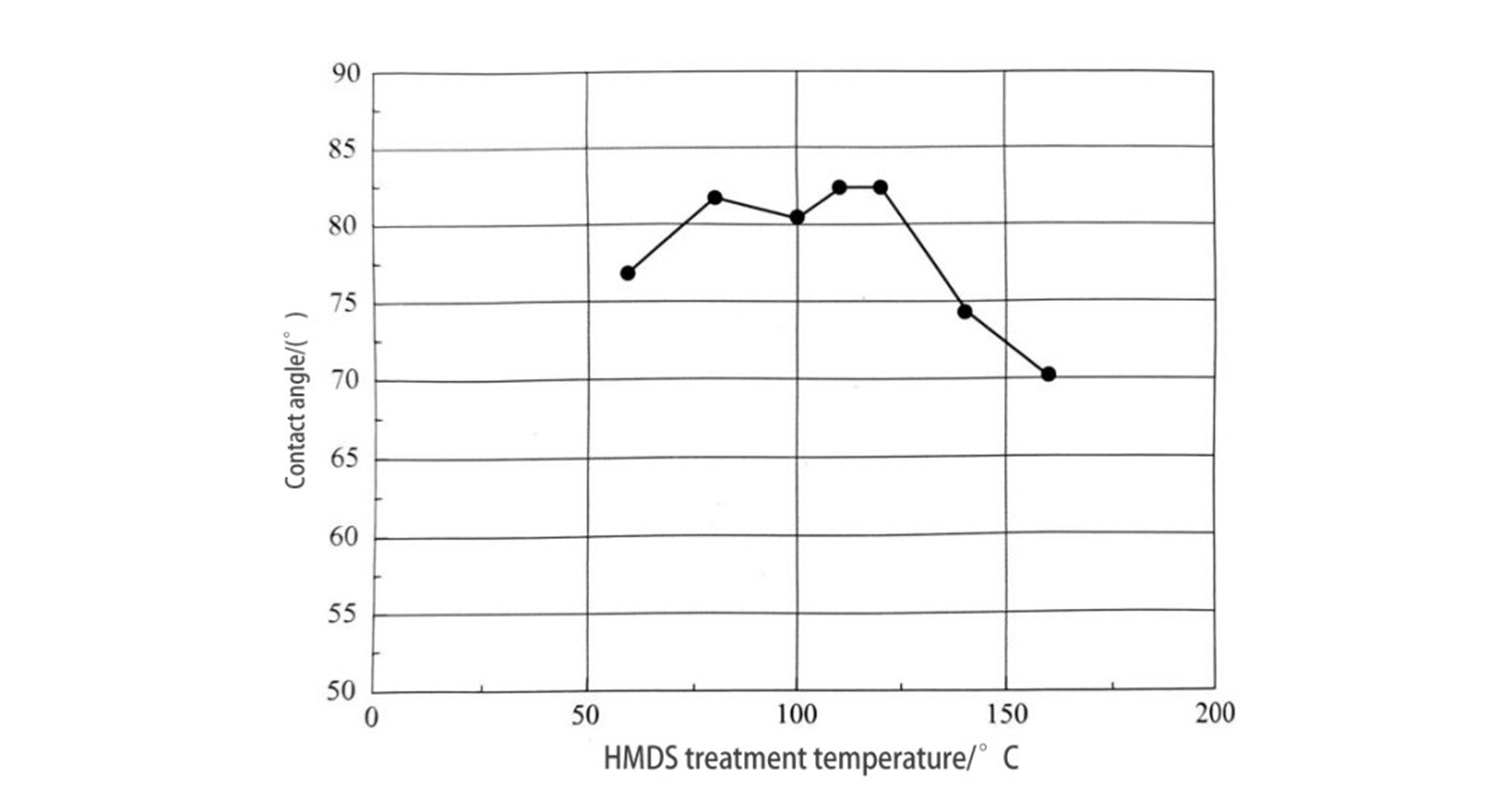
Figura 9: Relación entre a temperatura de tratamento do HMDS e o ángulo de contacto (tempo de tratamento 60 s)
O tratamento con HMDS realízase nun substrato de silicio cunha película de óxido para formar un patrón de fotorresistencia. Despois, a película de óxido é gravada con ácido fluorhídrico con un tampón engadido, e compróbase que despois do tratamento con HMDS, o patrón de fotorresistencia pódese evitar que se desprenda. A figura 10 mostra o efecto do tratamento con HMDS (o tamaño do patrón é 1um).
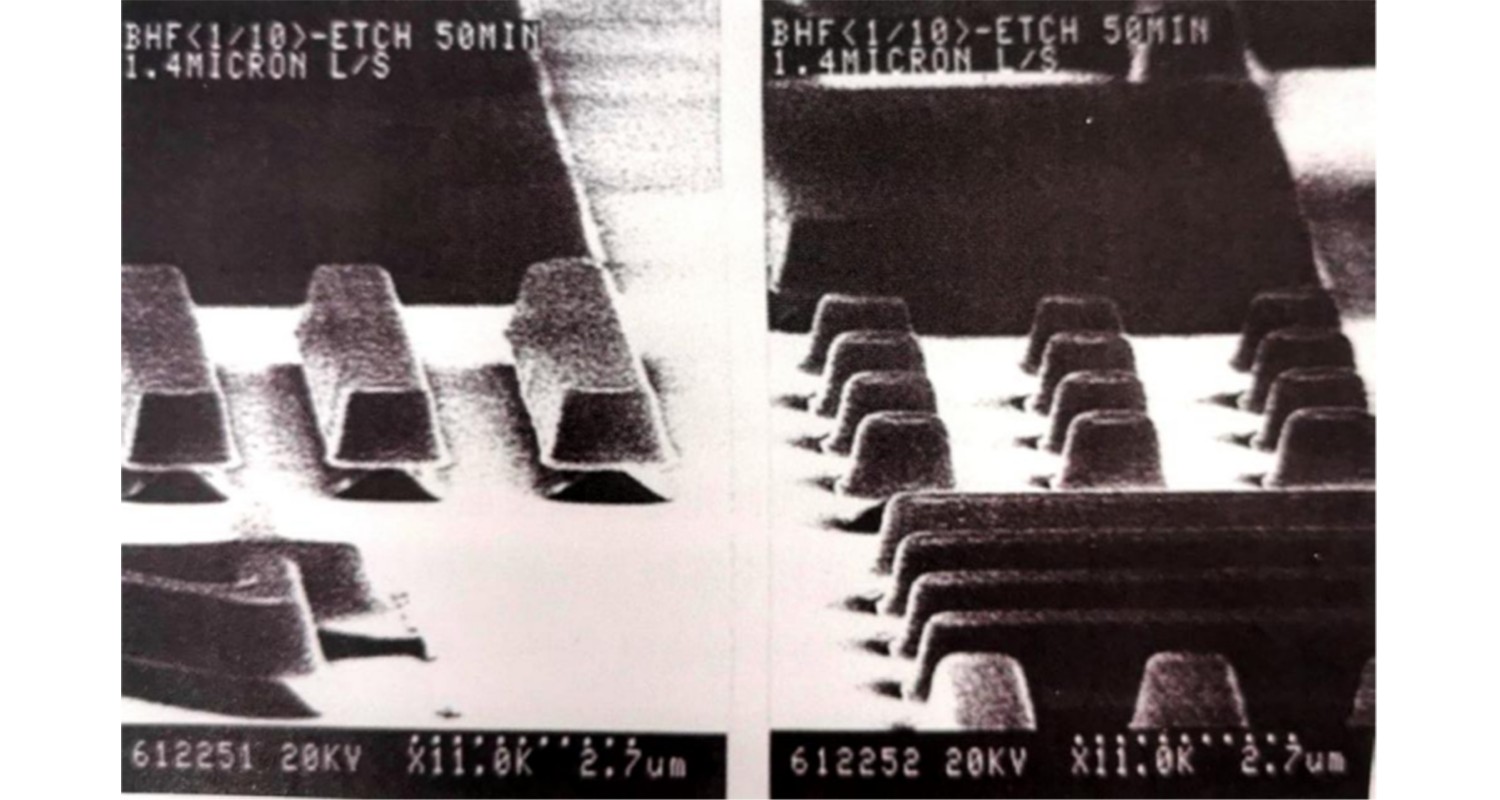
Figura 10: efecto do tratamento HMDS (o tamaño do patrón é 1um)
Precocción
Á mesma velocidade de rotación, canto maior sexa a temperatura de precocción, menor será o grosor da película, o que indica que canto maior sexa a temperatura de precocción, máis disolvente se evapora, o que resulta nun espesor de película máis fino. A figura 11 mostra a relación entre a temperatura previa á cocción e o parámetro A de Dill. O parámetro A indica a concentración do axente fotosensible. Como se pode ver na figura, cando a temperatura de precocción supera os 140 °C, o parámetro A diminúe, o que indica que o axente fotosensible se descompón a unha temperatura superior a esta. A figura 12 mostra a transmitancia espectral a diferentes temperaturas de precocción. A 160 °C e 180 °C, pódese observar un aumento da transmitancia no rango de lonxitudes de onda de 300-500 nm. Isto confirma que o axente fotosensible é cocido e descomposto a altas temperaturas. A temperatura de precocción ten un valor óptimo, que está determinado polas características da luz e a sensibilidade.
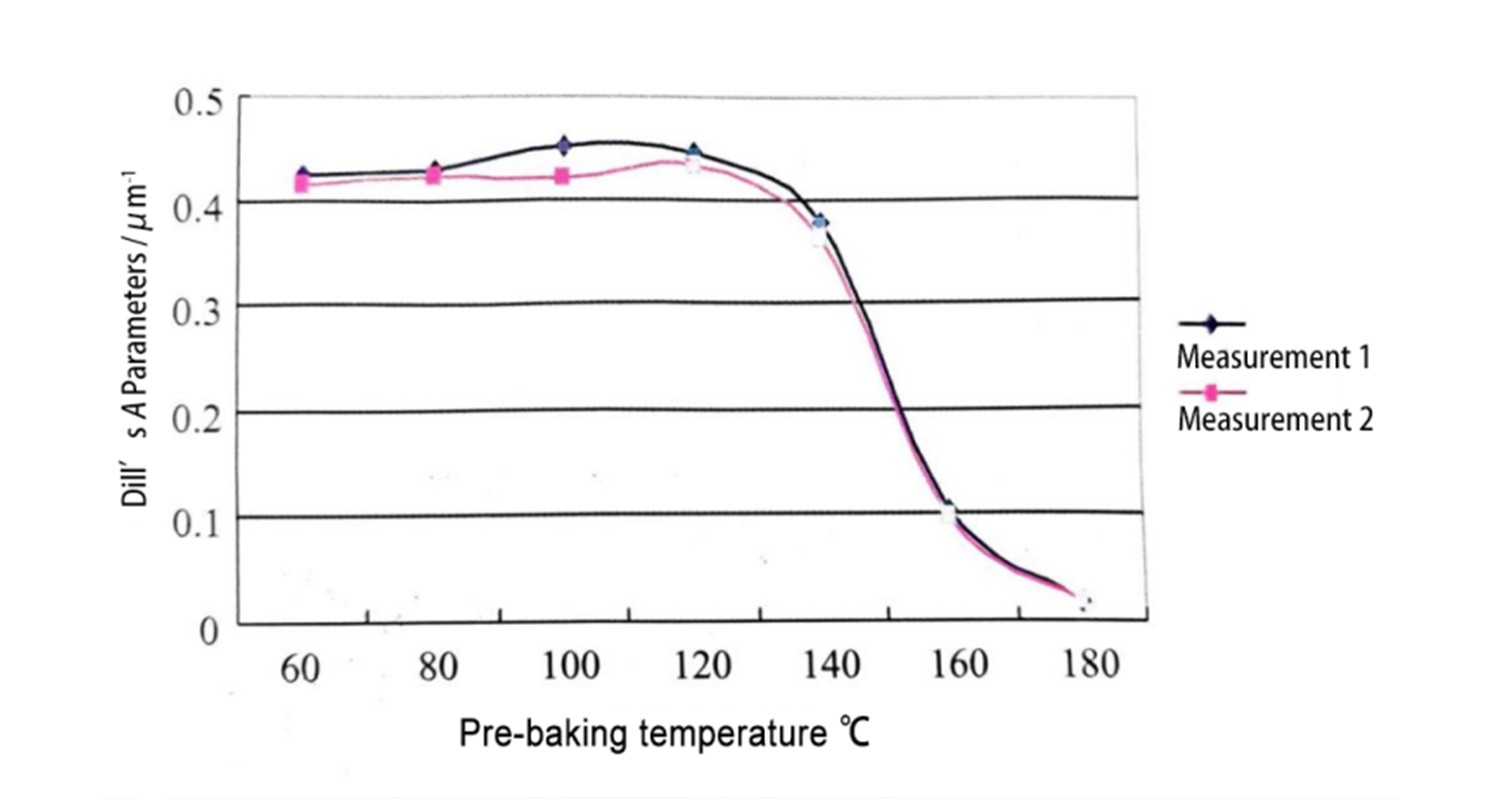
Figura 11: Relación entre a temperatura previa á cocción e o parámetro A de Dill
(valor medido de OFPR-800/2)
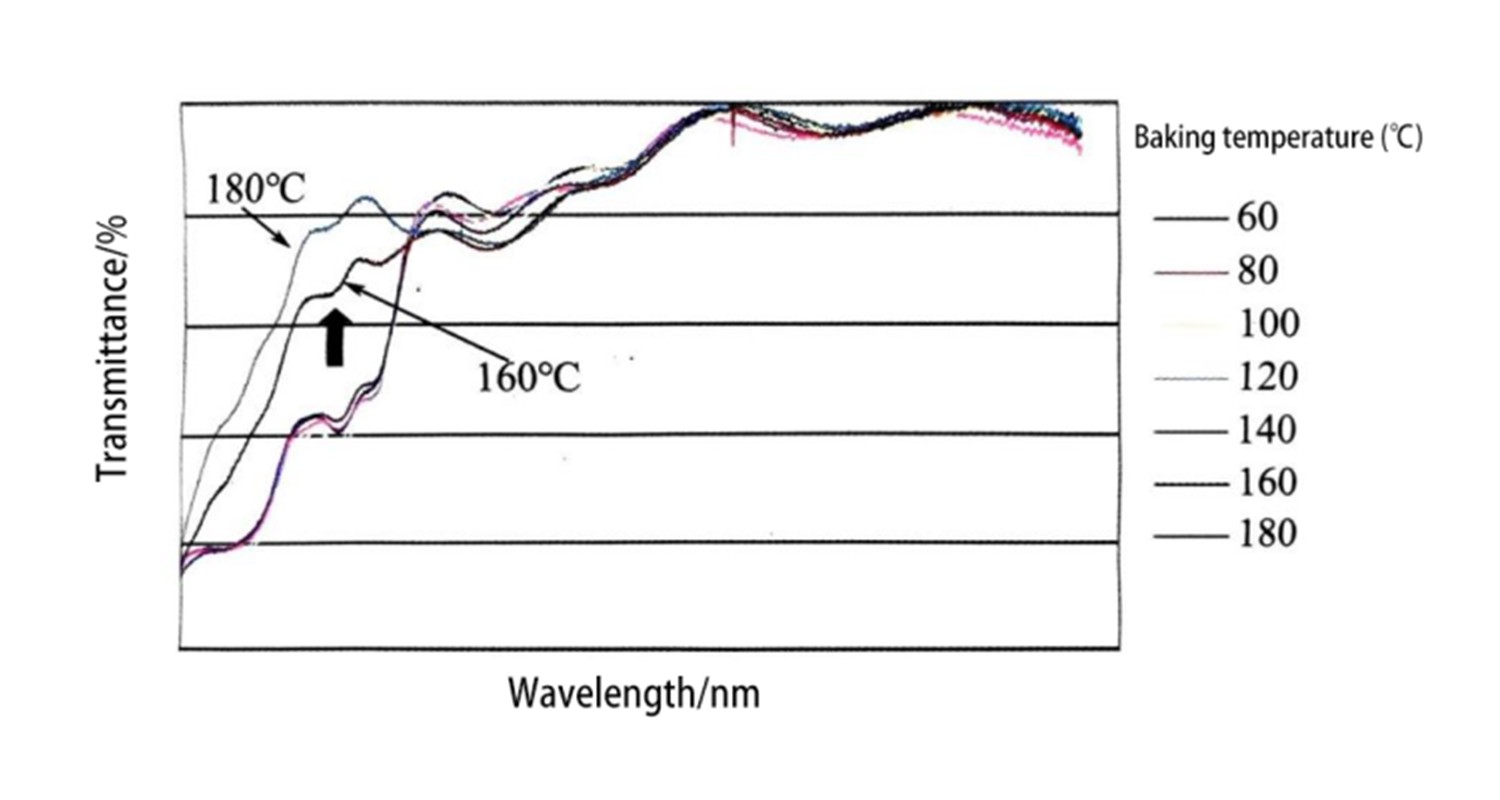
Figura 12: transmitancia espectral a diferentes temperaturas de precocción
(OFPR-800, espesor de película 1um)
En resumo, o método de revestimento por centrifugado ten vantaxes únicas como o control preciso do espesor da película, o alto rendemento dos custos, as condicións de proceso suaves e un funcionamento sinxelo, polo que ten efectos significativos na redución da contaminación, o aforro de enerxía e a mellora do rendemento dos custos. Nos últimos anos, o revestimento por centrifugación foi gañando cada vez máis atención e a súa aplicación estendeuse gradualmente a varios campos.
Hora de publicación: 27-novembro-2024