A cerámica de nitruro de silicio (Si₃N₄), como cerámica estrutural avanzada, posúe excelentes propiedades como resistencia a altas temperaturas, alta resistencia, alta tenacidade, alta dureza, resistencia á fluencia, resistencia á oxidación e resistencia ao desgaste. Ademais, ofrecen unha boa resistencia ao choque térmico, propiedades dieléctricas, alta condutividade térmica e un excelente rendemento de transmisión de ondas electromagnéticas de alta frecuencia. Estas excelentes propiedades completas fan que sexan amplamente utilizadas en compoñentes estruturais complexos, especialmente no aeroespacial e noutros campos de alta tecnoloxía.
Non obstante, o Si₃N₄, sendo un composto con fortes enlaces covalentes, ten unha estrutura estable que dificulta a sinterización a alta densidade só mediante a difusión en estado sólido. Para favorecer a sinterización, engádense axudas de sinterización, como óxidos metálicos (MgO, CaO, Al₂O₃) e óxidos de terras raras (Yb₂O₃, Y₂O₃, Lu₂O₃, CeO₂), para facilitar a densificación mediante un mecanismo de sinterización en fase líquida.
Actualmente, a tecnoloxía global dos dispositivos semicondutores avanza cara a tensións máis altas, correntes máis grandes e densidades de potencia maiores. A investigación sobre métodos para fabricar cerámica Si₃N₄ é extensa. Este artigo presenta procesos de sinterización que melloran eficazmente a densidade e as propiedades mecánicas completas das cerámicas de nitruro de silicio.
Métodos de sinterización comúns para cerámicas Si₃N₄
Comparación do rendemento das cerámicas de Si₃N₄ preparadas por diferentes métodos de sinterización
1. Sinterización reactiva (RS):A sinterización reactiva foi o primeiro método utilizado para preparar industrialmente cerámicas de Si₃N₄. É sinxelo, rendible e capaz de formar formas complexas. Non obstante, ten un longo ciclo de produción, que non é propicio para a produción a escala industrial.
2. Sinterización sen presión (PLS):Este é o proceso de sinterización máis básico e sinxelo. Non obstante, require materias primas de Si₃N₄ de alta calidade e moitas veces resulta en cerámicas con menor densidade, contracción significativa e tendencia a rachar ou deformarse.
3. Sinterización por prensa en quente (HP):A aplicación de presión mecánica uniaxial aumenta a forza motriz para a sinterización, permitindo que se produzan cerámicas densas a temperaturas 100-200 °C inferiores ás utilizadas na sinterización sen presión. Este método úsase normalmente para fabricar cerámicas en forma de bloque relativamente simples, pero é difícil cumprir os requisitos de espesor e forma dos materiais de substrato.
4. Sinterización de plasma con chispa (SPS):SPS caracterízase por unha sinterización rápida, un refinamento do gran e unhas temperaturas de sinterización reducidas. Non obstante, SPS require un investimento importante en equipos e a preparación de cerámicas Si₃N₄ de alta condutividade térmica a través de SPS aínda está en fase experimental e aínda non se industrializou.
5. Sinterización a presión de gas (GPS):Ao aplicar presión de gas, este método inhibe a descomposición cerámica e a perda de peso a altas temperaturas. É máis doado producir cerámica de alta densidade e permite a produción en lotes. Non obstante, un proceso de sinterización a presión de gas dun só paso loita por producir compoñentes estruturais cunha cor e estrutura interna e externa uniformes. Usar un proceso de sinterización en dous ou varios pasos pode reducir significativamente o contido de osíxeno intergranular, mellorar a condutividade térmica e mellorar as propiedades xerais.
Non obstante, a alta temperatura de sinterización da sinterización a presión de gas en dous pasos levou a investigación previa a centrarse principalmente na preparación de substratos cerámicos Si₃N₄ con alta condutividade térmica e resistencia á flexión a temperatura ambiente. A investigación sobre cerámicas Si₃N₄ con propiedades mecánicas amplas e propiedades mecánicas a altas temperaturas é relativamente limitada.
Método de sinterización en dous pasos a presión de gas para Si₃N₄
Yang Zhou e os seus colegas da Universidade Tecnolóxica de Chongqing utilizaron un sistema auxiliar de sinterización de 5% en peso de Yb₂O₃ + 5% en peso de Al₂O₃ para preparar cerámicas de Si₃N₄ utilizando procesos de sinterización a presión de gas dun paso e dous pasos a 1800 °C. As cerámicas Si₃N₄ producidas polo proceso de sinterización en dúas etapas tiñan maior densidade e mellores propiedades mecánicas completas. A continuación resúmese os efectos dos procesos de sinterización por presión de gas nunha e dúas etapas sobre a microestrutura e as propiedades mecánicas dos compoñentes cerámicos Si₃N₄.
Densidade O proceso de densificación de Si₃N₄ normalmente implica tres etapas, con superposición entre as etapas. A primeira etapa, a reordenación das partículas, e a segunda, a disolución-precipitación, son as etapas máis críticas para a densificación. O tempo de reacción suficiente nestas fases mellora significativamente a densidade da mostra. Cando a temperatura de pre-sinterización para o proceso de sinterización en dous pasos se establece en 1600 °C, os grans de β-Si₃N₄ forman un marco e crean poros pechados. Despois da presinterización, o quecemento adicional a alta temperatura e presión de nitróxeno promove o fluxo e o recheo en fase líquida, o que axuda a eliminar os poros pechados, mellorando aínda máis a densidade da cerámica Si₃N₄. Polo tanto, as mostras producidas polo proceso de sinterización en dous pasos mostran unha maior densidade e densidade relativa que as producidas pola sinterización nun paso.
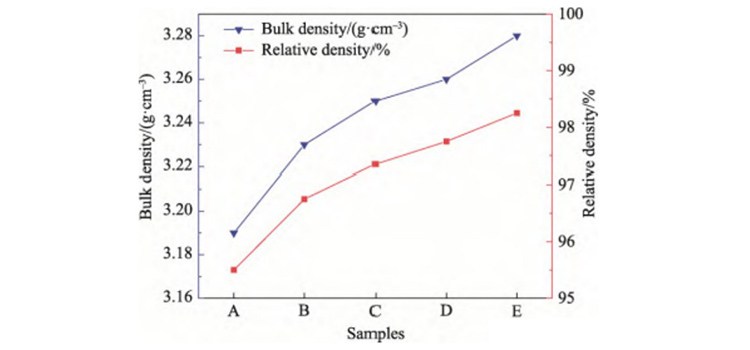
Fase e microestrutura Durante a sinterización nun paso, o tempo dispoñible para a reordenación das partículas e a difusión do límite do gran é limitado. No proceso de sinterización en dúas etapas, o primeiro paso realízase a baixa temperatura e baixa presión do gas, o que amplía o tempo de reordenación das partículas e resulta en grans máis grandes. A temperatura é entón aumentada ata a fase de alta temperatura, onde os grans seguen crecendo a través do proceso de maduración de Ostwald, obtendo cerámica de Si₃N₄ de alta densidade.
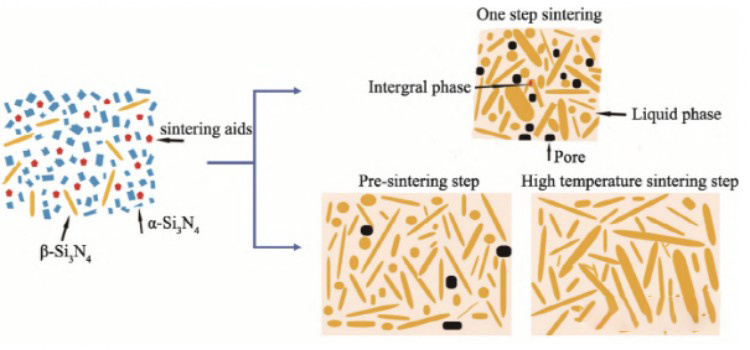
Propiedades mecánicas O reblandecemento da fase intergranular a altas temperaturas é a razón principal da redución da resistencia. Na sinterización dun paso, o crecemento anormal dos grans crea pequenos poros entre os grans, o que impide unha mellora significativa na resistencia a altas temperaturas. Non obstante, no proceso de sinterización en dous pasos, a fase de vidro, distribuída uniformemente nos límites dos grans, e os grans de tamaño uniforme melloran a resistencia intergranular, obtendo unha maior resistencia á flexión a alta temperatura.
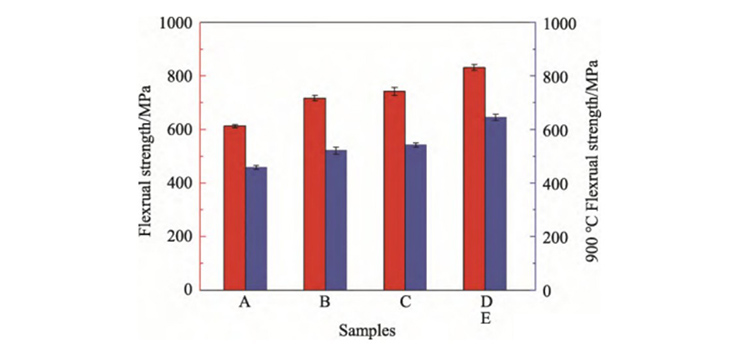
En conclusión, a retención prolongada durante a sinterización nun só paso pode reducir eficazmente a porosidade interna e lograr unha cor e estrutura internas uniformes, pero pode provocar un crecemento anormal do gran, o que degrada certas propiedades mecánicas. Empregando un proceso de sinterización en dúas etapas (utilizando a presinterización a baixa temperatura para prolongar o tempo de reordenación das partículas e manter a alta temperatura para promover un crecemento uniforme do gran), unha cerámica de Si₃N₄ cunha densidade relativa do 98,25 %, microestrutura uniforme e excelentes propiedades mecánicas completas. pódese preparar con éxito.
Nome | Substrato | Composición da capa epitaxial | Proceso epitaxial | Medio epitaxial |
Silicio homoepitaxial | Si | Si | Epitaxia en fase de vapor (VPE) | SiCl4+H2 |
Silicio heteroepitaxial | Zafiro ou espinela | Si | Epitaxia en fase de vapor (VPE) | SiH₄+H₂ |
GaAs homoepitaxial | GaAs | GaAs GaAs | Epitaxia en fase de vapor (VPE) | AsCl₃+Ga+H₂ (Ar) |
GaAs | GaAs GaAs | Epitaxia de feixe molecular (MBE) | Ga+As | |
GaAs heteroepitaxial | GaAs GaAs | GaAlAs/GaAs/GaAlAs | Epitaxia en fase líquida (LPE) Fase de vapor (VPE) | Ga+Al+CaAs+H2 Ga + Ash3+ PH3+CHl+H2 |
GaP homoepitaxial | GaP | GaP(GaP;N) | Epitaxia en fase líquida (LPE) Epitaxia en fase líquida (LPE) | Ga+GaP+H2+(NH3) Ga+GaAs+GaP+NH3 |
Superreticular | GaAs | GaAlAs/GaAs (ciclo) | Epitaxia de feixe molecular (MBE) MOCVD | Ca,As,Al GaR₃+AlR3+AsH3+H2 |
InP homoepitaxial | InP | InP | Epitaxia en fase de vapor (VPE) Epitaxia en fase líquida (LPE) | PCl3+In+H2 In+InAs+GaAs+InP+H₂ |
Epitaxia Si/GaAs | Si | GaAs | Epitaxia de feixe molecular (MBE) MOGVD | Ga, As GaR₃+AsH₃+H₂ |
Hora de publicación: 24-12-2024